- Glencore
- Media and Insights
- Insights
- Recycling towards a circular economy
Recycling towards a circular economy
As the world’s population increases and economies continue to develop, electrifying our supply chain of energy has become increasingly important to address climate challenges by supporting the shift towards renewable energy and zero-carbon.
Moving from a combustion technology to an electrical technology requires a lot of metals. Copper is important for electrical transmission and nickel and cobalt are vital in the chemistries of current battery technology.
These commodities will need to be available in large amounts in order for the transition to actually take place, leading to higher demand. The primary sources such as mining and concentrates are not going to be enough to supply that demand. Recycling will play an essential role in moving towards a circular economy.
Recovering transition metals from end-of-life electronics and batteries
Glencore is one of the companies leading the charge in the recycling of copper, nickel, cobalt, and precious metals. Our operations were among the first to discover how to process end-of-life electronics, and we have been one of the leading recyclers of metals ever since.
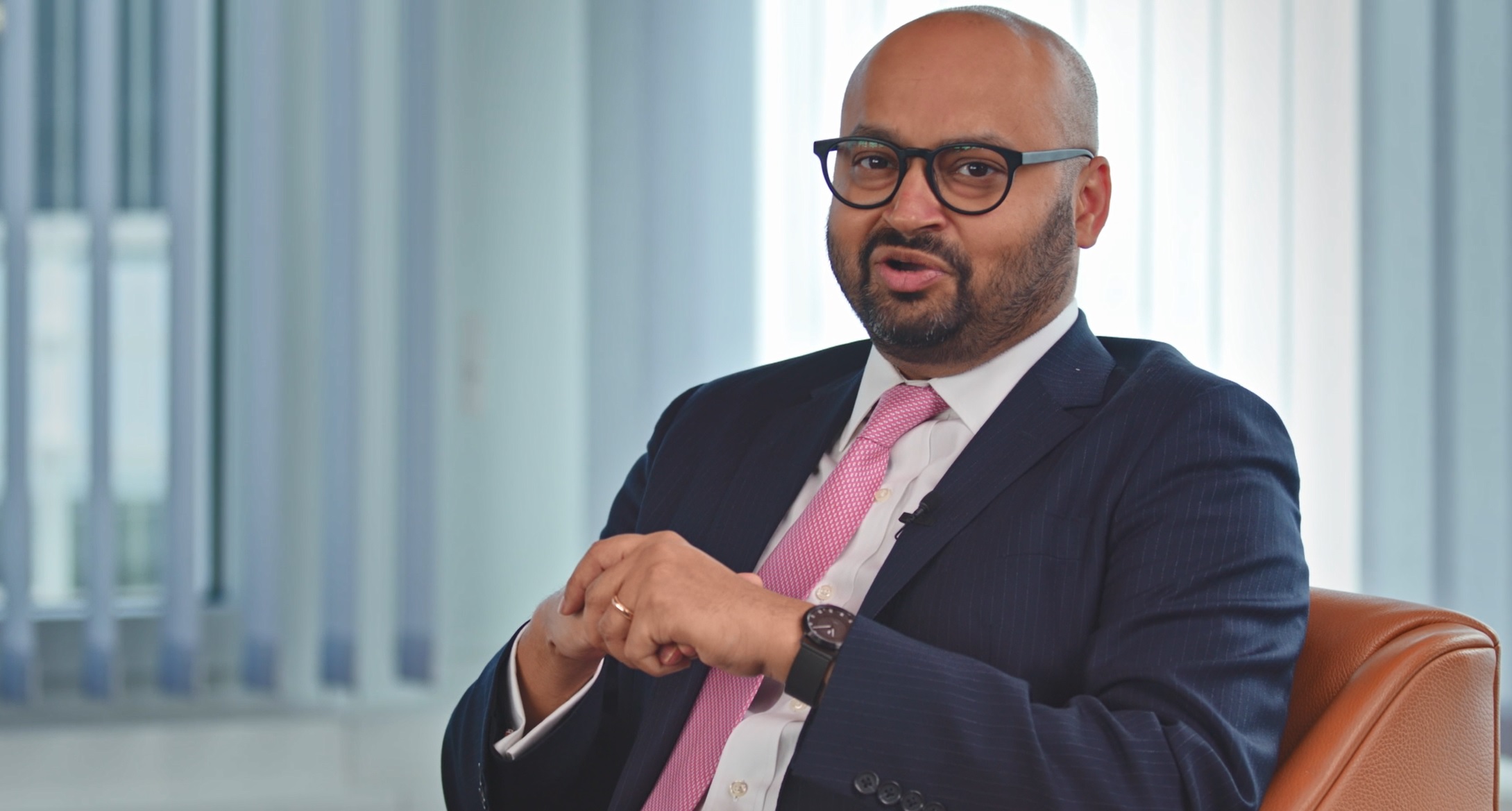
When I tell people we do a lot of recycling, sometimes they are surprised, and I say: “It’s the Glencore you don’t know."
Kunal Sinha - Head of Recycling, Glencore
The history of our recycling business goes back over 75 years. Our Horne Smelter in Rouyn-Noranda started recycling in the 1940s, and in the 1980s, became one of the first smelters in the world to pioneer the recovery of copper and precious metals from discarded electronics. While experimental in the early days, it has today grown from a side interest to a core functionality for Glencore.
Our Integrated Nickel Operations (INO) in Sudbury, Canada began recycling in 1990. Initially, the facility processed super-alloy scrap from the aerospace sector, before expanding to include other materials. Today, it processes secondary feed including end-of-life materials, production scrap and waste streams making it one of the largest processors of secondary nickel and cobalt bearing materials in the world.
We started taking end-of-life electronics in the 80s, and then we evolved with that, and today we are processing around 100,000 tonnes of recycling each and every year.
Jeremie Blanchette - Commercial Superintendent, Glencore – Horne Smelter, Rouyn-Noranda, Quebec
Redefining waste as a resource
E-scrap is the fastest growing waste category in the world through growing demand and shorter life-cycles for items such as cell phones and tablets. And through the growth of the EV market, with more giga factories being built around the world, the need to recycle those batteries will continue to accelerate in future. If these materials weren’t recycled, they would end up in landfill and be lost forever.
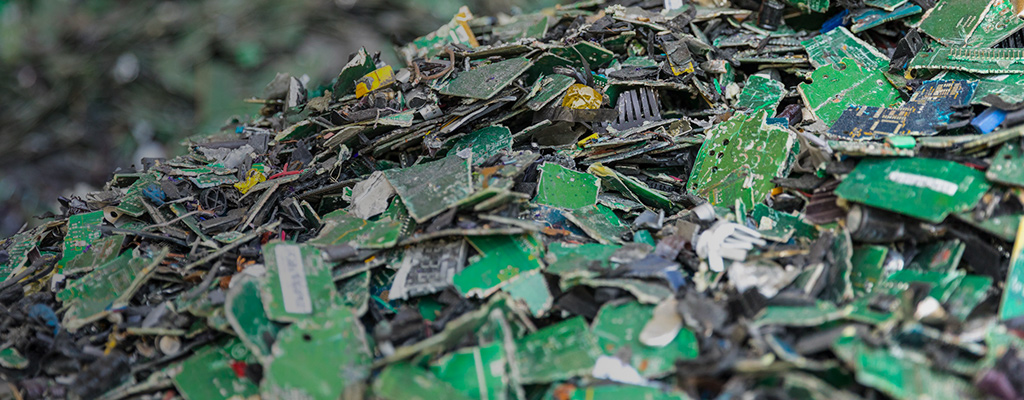
Rather than calling it a waste, one can call it “the urban mine”.
John Pellegrini - Raw Materials Manager, Glencore – Pittsburgh
Part of the challenge is thinking of end-of-life products not as waste but a resource. The moment materials are labelled as waste, society has a different connotation. At Glencore, we see these post-consumer materials as a valuable resource that will help supply the increasing demand for vital transition metals in support of transforming the energy supply chain and the world’s net zero ambition.
With world class smelters and refineries in place, Glencore is in a great position because we are sharing in the scale of our metallurgical facilities. We want to be the stewards of these products for their lifetimes.
Designing for circularity
The circular economy is a way of thinking, a way of building things and the process of recycling materials in a way that they can be reused over and over again. And it starts from the engineering and design of the products that we use every day.
It's essential to start building recyclability into those products to enforce the concept of a circular economy. Whatever product reaches the end of its life can be transformed into a new product.
We want to be able to safely move those batteries, treat those batteries and return the metals back to producers so that they can continue to grow their businesses.
Russel Mascarenhas - Trader, Glencore – Baar, Switzerland
Together with our partners, we helped establish the Circular Electronics Partnership – the first private sector alliance for circular electronics. This partnership allows us as a smelter and a refiner to speak directly to an electrical OEM. Otherwise, these two parties have no reason to connect as we sit at very opposite ends of a linear supply chain. Now, we are sitting next to each other and are having conversations on how to design for circularity.
This way, we can bring transition metals back to our platform, recycle them, and make them available again for reuse. And not just after their first life, second life, or the third life, but multiple times over. Our in-house processing capacity provides the infrastructure to help bring the circular economy to life.